Explore our Services
From enquiry to solution, from problem to satisfaction, we do everything we can to exceed your expectations. Your feedback is invaluable to us and we are always willing to listen to your needs to ensure you have the best possible experience with our products and services.
Installation
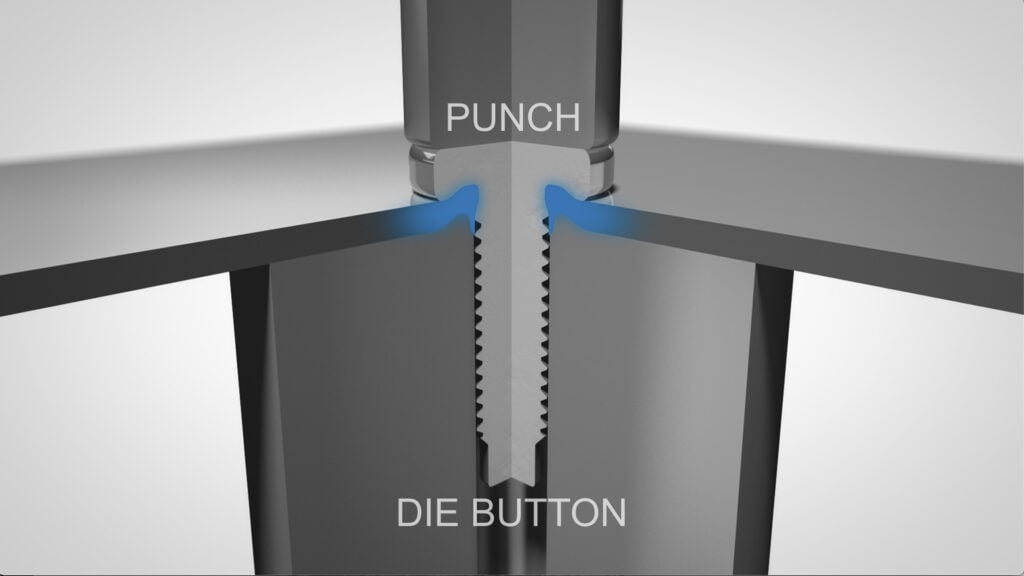
Commissioning
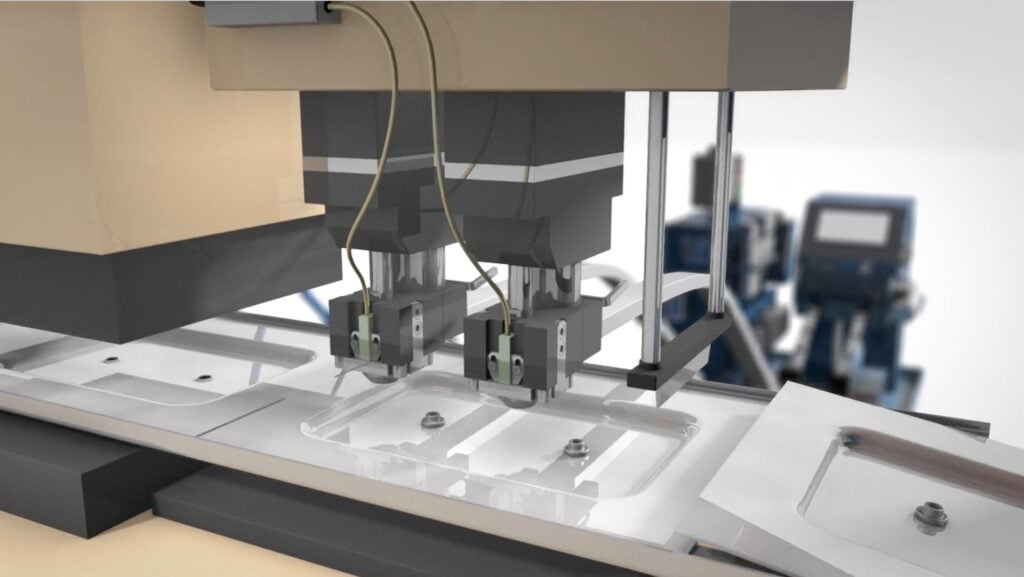
Process Optimisation

Training
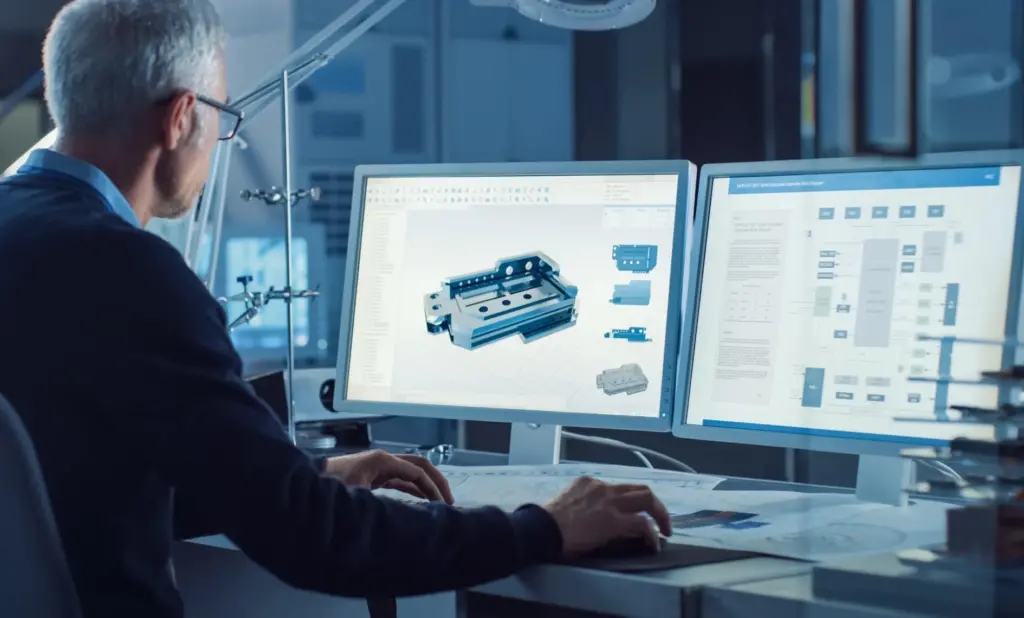
Maintenance
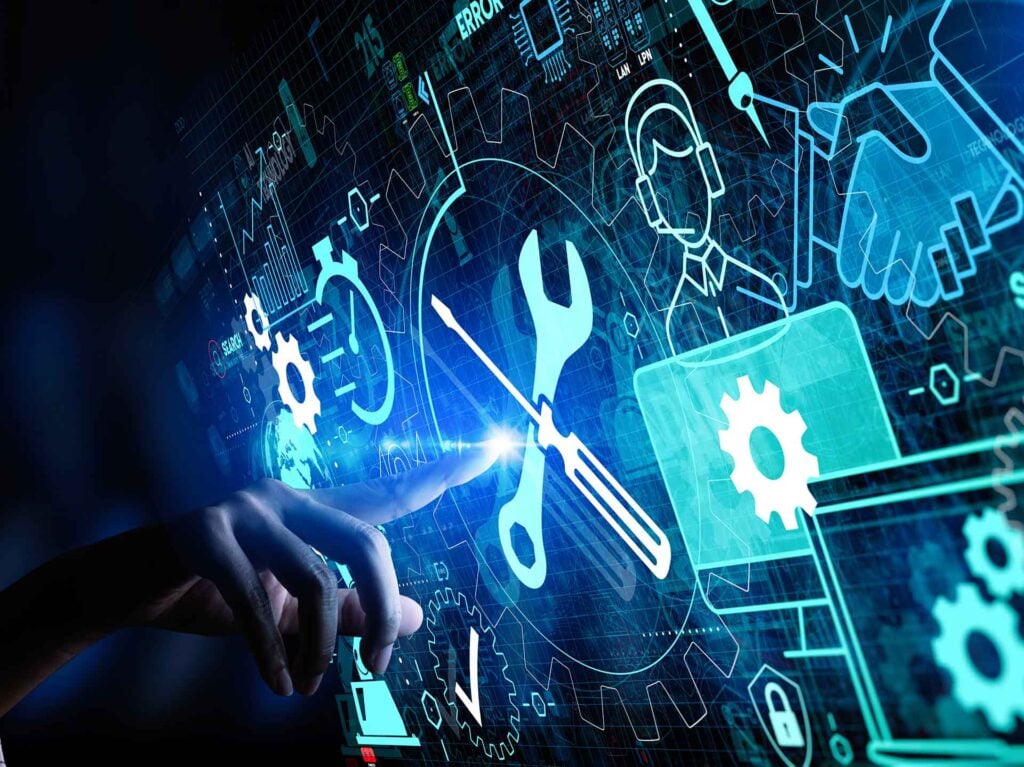
Service Contracts
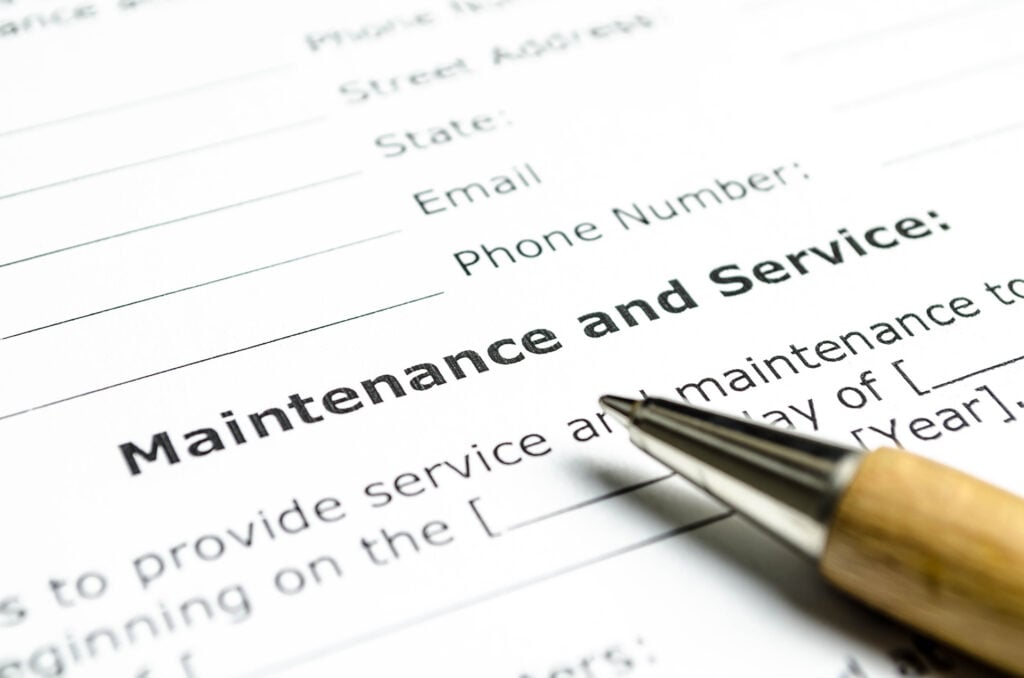
Service Products
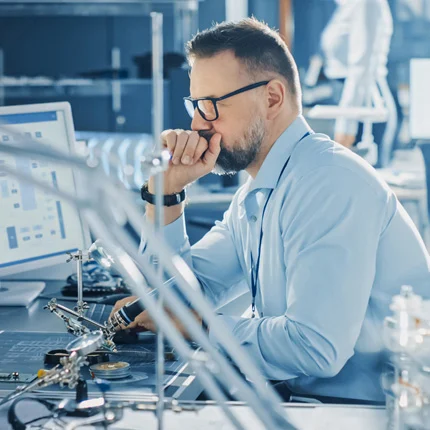
Contact us
View our contact page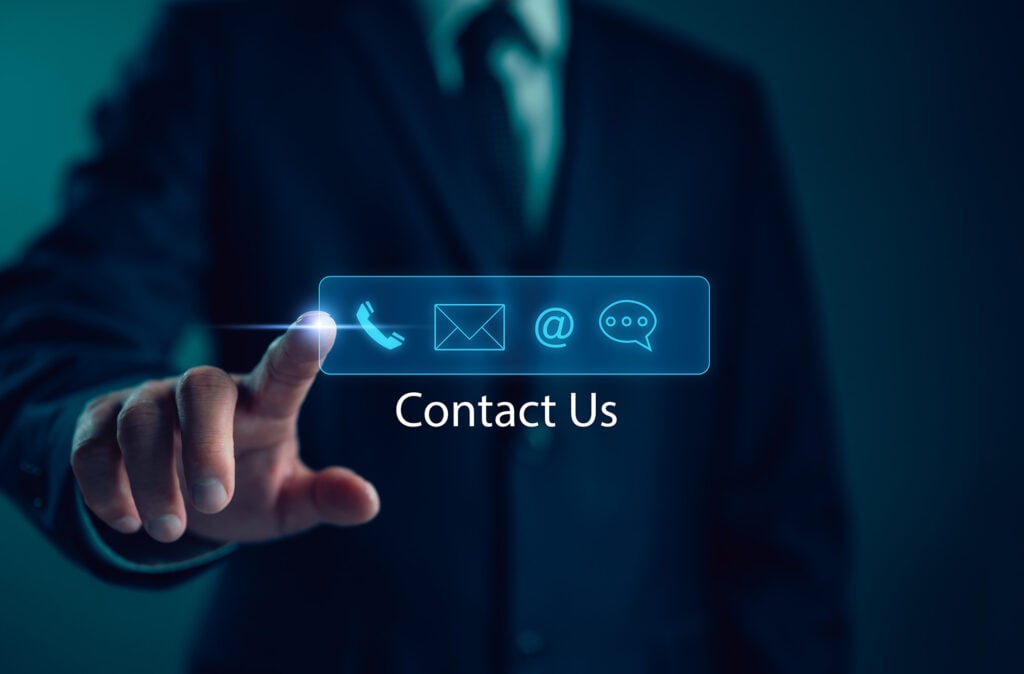